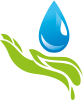
October 2023
New Requirements for 2023/24
The revised LCA Service Delivery Standard for Water Treatment launched on the 1st of July 2023 with no new requirements for Members.
There are some minor changes to the detail in section D that brings the different service standards more in line with each other. Members will need to make sure quotation and other communication templates used to deal with this part of the standard are updated.
In auditing going forward we are moving away from non-legionella specific items and trying to focus attention on core issues. If Members have any feedback on what is most important in the real world and where we should focus audit, please let us know. The 2023 auditing document including checklists is available now with a highlighted changes version.
Common Failings and Areas of Focus
Some common failings we see in Water Treatment are:
- Not having an adequate process of capturing pre-quote information
- Shortcomings in procedure to design or evaluate a water treatment programme
- Weaknesses in setting of control parameters
- Lack of consistency in application of control parameters
- No specifics on the testing equipment to be used
- No consideration of the compatibility of products when dosed together
These all lead to weaknesses in the water treatment programme, a potential loss of legionella control and legal exposure for LCA Members. Our intention at audit is to identify and close weaknesses in our Members’ process.
Pre-quote Information
You wouldn’t calculate a fuel charge without knowing how far you must drive or the MPG the vehicle will achieve. Water treatment is no different. Under requirement 3.2 of the Code of Conduct Members are required to gather information to be able to design a service. Water treatment is arguably the most involved and complex control measure to design and requires specific and detailed information. We expect the information to be obtained from survey, conversation with prospective clients, tender specifications or other sources and documented. If it is unavailable and assumptions are made, we expect to see the basis of those assumptions detailed in written client agreements.
If the information is not known, it is impossible to design a programme that complies with the LCA Service Delivery Standard.
Design Procedures
The LCA requires a consistent, considered approach in design of water treatment programmes. We sometimes see the preference of each individual being the design process or a continuation of an existing programme with no evaluation. The LCA expectation here is for a design procedure that should lead anybody using it, with the same input data (that pre-quote detail again!), to the same or at least a similar programme design. Selection of chemicals for hard or soft waters, system metallurgy, etc.
Taking over an existing water treatment programme without using your own procedure to check it is valid and effective leaves you with the liability for that programme. If taking over a water treatment programme you should always check it against what you would do when designing a new programme.
Setting of Control Parameters and Consistency in Application
The controls are part of the design of the water treatment programme and are sometimes lacking. Quoting from HSG274 info box 1.5 on oxidising biocides might be fine provided all aspects are considered and understood. 1-2ppm bromine may not be enough at higher pH ranges – read all of the info box not just the headline numbers! Remember that the HSE guidance documents are not water treatment manuals! Your procedure needs to detail how you come up with the control limits you apply.
We sometimes see systems operating outside their control limits with commentary around the lack of importance of that control limit and no actions taken. Control limits should be useful and where they are not appropriate they should be reviewed and changed.
Testing Equipment
Testing equipment is critical to determine if a system is operating in control or not. LCA Members’ procedures should consider the level of accuracy and precision required to determine that control, and detail suitable test equipment. We occasionally see the use of low precision testing equipment that is totally unsuitable for the task. More commonly we see a lack of detail in procedures on what equipment is intended to be used.
Product Compatibility
We occasionally see chemicals being used together that are incompatible. For example, a readily oxidisable inhibitor being used with an oxidising biocide. Far more commonly we see a shortcoming in procedure. The procedure should drive safe product selection for compatible products. Procedures should ensure the chemicals used in water treatment programmes play well together.
If you recognise some of the above in your work, check your process, procedure, water treatment chemical selection guides, programming guides and templates as soon as possible.
v2 (updated 13-10-23)